There is no item in your cart
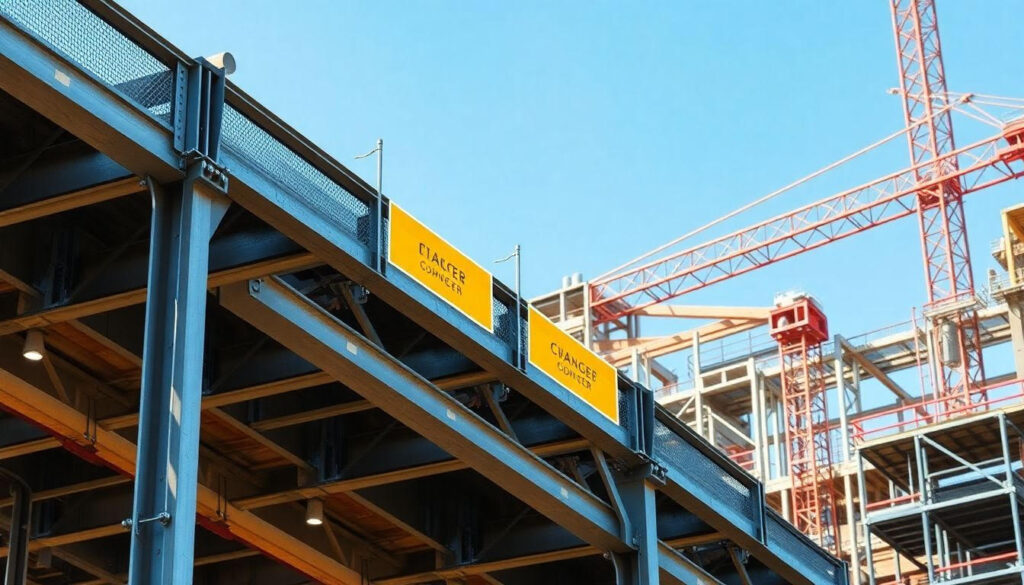
Steel Detailing Change Orders: How to Protect Your Project Budget & Schedule
Ever seen a project grind to a halt because of one small change? A missing beam, a misplaced bolt – suddenly, everything’s delayed and over budget. Project managers, contractors, and fabricators all share the same pain. Change orders. They can be a major headache, especially in steel detailing.
This article is your guide to understanding steel detailing change orders. You’ll learn how to manage them and keep them from wrecking your project’s finances and schedule. Let’s dive in.
Understanding Steel Detailing Change Orders
A steel detailing change order is an adjustment to the original steel detailing plans. These changes happen after the initial design phase. They can be due to several reasons. They impact the project’s cost and timeline.
Common Causes of Change Orders
Lots of things can lead to change orders. Errors in the original blueprints are frequent. Sometimes, clashes are found during the steel detailing process. The client or architect might also request changes.
Imagine a blueprint shows a support beam connecting to a wall. But, the wall’s structural engineer says it can’t handle the load. This design error leads to a change order. The steel detailer must then redesign the connection. This fix adds time and expense to the project.
The Change Order Process: A Step-by-Step Overview
The standard change order process involves a few steps. First, someone spots the need for a change. Then, they notify the relevant parties. Next comes pricing the change. After approval, the change is put into action.
Document every step. It can’t be emphasized enough. This helps you keep track of costs. It also helps to avoid disagreements later.
The Financial Impact of Steel Detailing Changes
Change orders hit your wallet in a few ways. There are direct costs for labor, materials, and rework. Then there are indirect costs tied to delays. These costs can quickly add up.
Direct Costs: Labor, Materials, and Rework
Direct costs are easy to see. Extra hours for detailing cost more. Buying more materials is a clear expense. Fixing mistakes in the shop or field costs money, too.
For example, a change order might require 20 extra hours of detailing. At $75 per hour, that’s $1,500. You might also need $500 in new steel. Then, another $1,000 for shop labor to make the fix. That single change order has now cost $3,000.
Indirect Costs: Delays and Disruption
Delays can be expensive. A change order could push back the whole project. This can mean you pay liquidated damages. Other trades might also be affected, which can create bigger problems.
Estimate costs carefully. Plan for surprises. Having a budget set aside for unexpected costs is vital. This will help protect the project’s financial health.
Mitigating the Impact on Project Schedule
Change orders don’t have to derail your project. With the right strategies, you can keep delays to a minimum. Here are some tactics for success.
Proactive Communication and Collaboration
Talk, talk, talk. Talk early and often. It’s important that the design team, detailer, fabricator, and contractor are all on the same page.
Hold regular meetings. Use BIM (Building Information Modeling). These tools help everyone communicate clearly. They catch issues early.
Utilizing Advanced Technology and Software
BIM can be a game-changer. It helps spot problems before they become costly change orders. Other software can also make the change order process smoother.
BIM software can detect clashes. A clash is when two elements occupy the same space. Finding these clashes early saves time and money.
Best Practices for Managing Steel Detailing Change Orders
Here’s some practical advice for managing change orders well. From start to finish, these tips can help.
Comprehensive Contract Review and Negotiation
Your contract is key. It must clearly define the scope of work. It must also detail the change order procedures. Pricing needs to be spelled out.
Get legal advice. A lawyer can help you negotiate a fair contract. This will give you the best protection possible.
Accurate Documentation and Record-Keeping
Keep good records. Track all communication. Log every change. Note all related costs.
Use project management software. It can help you track change orders. Good documentation protects everyone.
Preventing Steel Detailing Change Orders
The best change order is the one that never happens. These steps can reduce the risk of change orders.
Thorough Initial Design and Coordination
Start with solid plans. Accurate and complete designs are crucial. They minimize errors.
Implement a design review process. Have experienced eyes check the plans. This catches mistakes early.
Engaging Experienced and Qualified Detailers
Hire the right people. Skilled steel detailers spot problems early. They avoid mistakes.
Check their background. See what experience they have. Verify they are qualified.
Conclusion
Steel detailing change orders can be a big challenge. But, by understanding them, you can manage them. This will keep your project on track. Proactive management and prevention are key. Take the steps we’ve discussed. Protect your project’s budget and schedule.
Leave A Comment